Как увеличить срок службы молотков дробилки
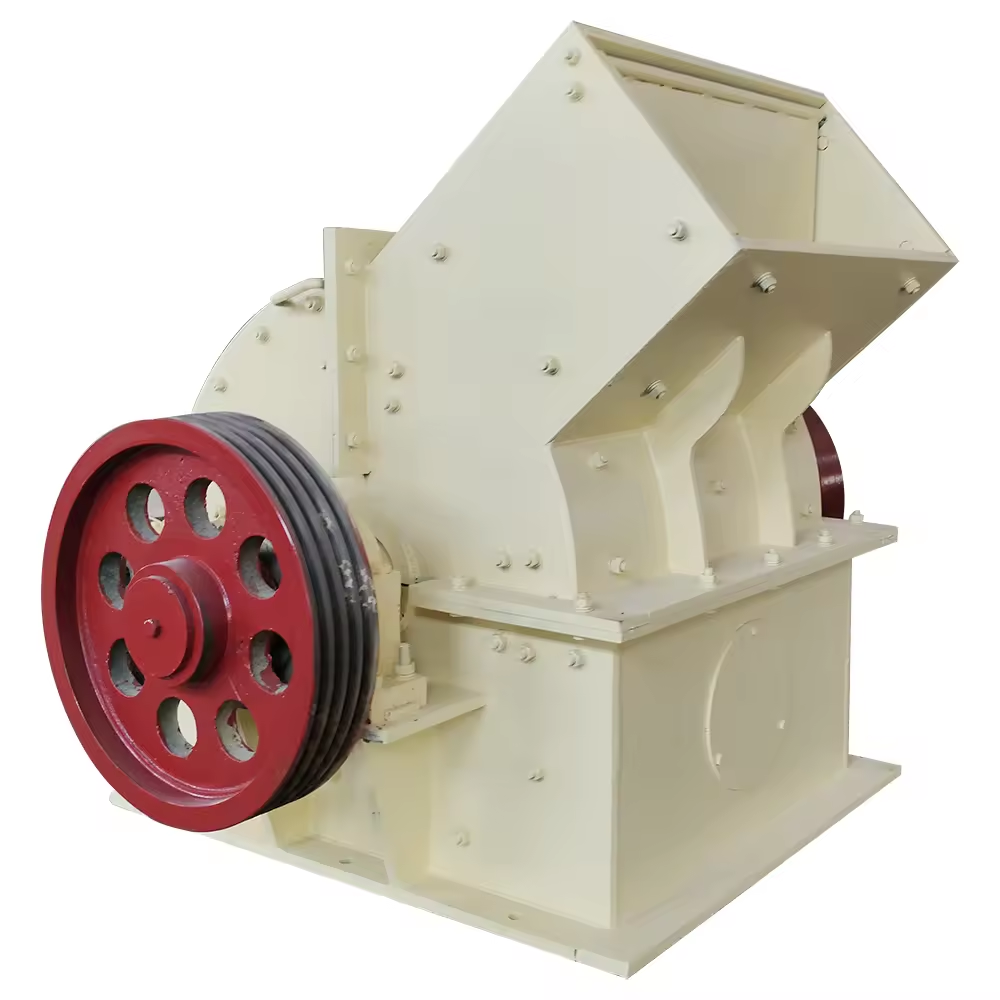
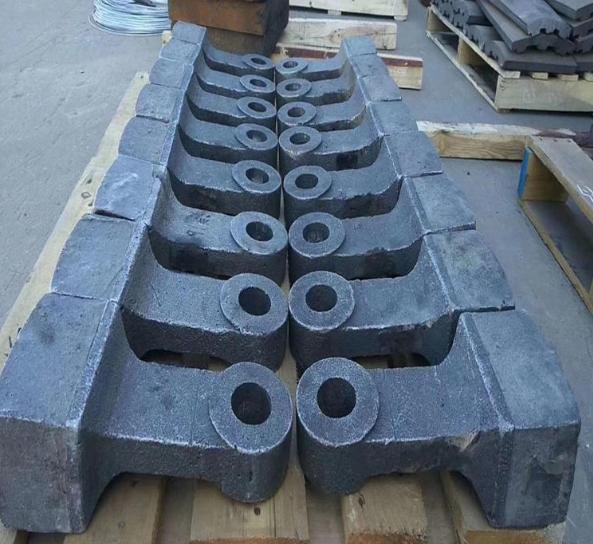
Молотки для дробилок играют решающую роль в производительности и эффективности дробильной машины. Они подвергаются высокому уровню износа, особенно в таких отраслях, как горнодобывающая, цементная и строительная. Долговечность молотков дробилок напрямую влияет на общие эксплуатационные расходы, время простоя и производительность. Поэтому продление срока службы молотков дробилок является приоритетной задачей для многих промышленных предприятий. В этой статье мы рассмотрим различные стратегии и методы, которые могут помочь увеличить срок службы молотков дробилок.
1. Выбирайте высококачественные материалы
Долговечность молотка дробилки начинается с качества материала, из которого он изготовлен. Высококачественные материалы необходимы для обеспечения устойчивости к износу, ударам и высоким температурам. Распространенные материалы, используемые для изготовления молотков дробилок, включают:
- Высокомарганцевая сталь: Это один из наиболее широко используемых материалов для молотков дробилок. Он обладает отличной стойкостью к ударам и истиранию и выдерживает большие нагрузки, возникающие при дроблении.
- Высокохромистая сталь: Известная своей превосходной твердостью и износостойкостью высокохромистая сталь - еще один хороший выбор для молотков дробилок. Она хорошо работает в условиях, связанных с абразивными материалами.
- Легированная сталь: Некоторые молотки изготавливаются из легированной стали с добавлением таких элементов, как никель, хром и молибден, для повышения их прочности и устойчивости к ударам.
- Карбид вольфрама: Для работы в экстремальных условиях часто используются молотки с покрытием из карбида вольфрама благодаря их исключительной твердости и долговечности, особенно при работе с высокоабразивными или коррозионными материалами.
Выбор правильного материала в зависимости от типа измельчаемого материала и условий эксплуатации - первый шаг к максимальному увеличению срока службы молотков дробилки.
2. Правильное обслуживание и проверка
Регулярное техническое обслуживание и осмотр молотков дробилок - важнейшее условие поддержания их в оптимальном состоянии. К числу основных методов технического обслуживания относятся:
- Регулярный осмотр: Часто осматривайте молотки на предмет признаков износа, трещин или повреждений. Это поможет обнаружить проблемы, которые могут привести к преждевременному выходу из строя, и своевременно произвести замену или ремонт.
- Смазка: Правильная смазка движущихся частей уменьшает трение и износ, помогая предотвратить чрезмерный износ молотков. Убедитесь, что подшипники и другие детали хорошо смазаны.
- Уборка: Периодически очищайте дробилку, чтобы удалить мусор, грязь и скопления, которые могут повлиять на работу молотка. Это поможет сохранить эффективность и предотвратить преждевременный износ, вызванный загрязнениями.
- Балансировка: Дисбаланс ротора или молотка может привести к неравномерному износу. Регулярно проверяйте баланс и выравнивание ротора и молотков дробилки, чтобы предотвратить чрезмерную нагрузку на молотки и их износ.
3. Оптимизированные условия эксплуатации
Молотки дробилки могут быстро изнашиваться, если дробилка работает не в оптимальных условиях. Очень важно обеспечить эффективное использование машины и соблюдение рекомендуемых параметров.
- Избегайте перегрузок: Перегрузка дробилки может привести к тому, что молотки будут работать интенсивнее, чем они предназначены, что приведет к их быстрому износу и возможному выходу из строя. Убедитесь, что дробилка загружена в пределах ее заданной мощности.
- Оптимальная скорость: Работа дробилки на правильной скорости очень важна. Работа на более высоких скоростях, чем рекомендовано, может привести к чрезмерному износу молотков, а работа на более низких скоростях может снизить эффективность дробления.
- Правильный размер корма: Убедитесь, что исходный материал соответствует размерам дробилки, и это также уменьшит износ. Слишком крупный или слишком мелкий материал может заставить молотки работать неэффективно, что приведет к преждевременному износу.
4. Конструкция и конфигурация молота
Конструкция молотка дробилки играет важную роль в его долговечности. Оптимизация конструкции и конфигурации молотка может повысить его производительность и уменьшить износ.
- Изменения в конструкции: В некоторых современных дробилках молотки имеют особые контуры или узоры, которые помогают распределять ударную нагрузку более равномерно, уменьшая локальный износ.
- Вес молотка: Вес молотков влияет на процесс дробления. Более тяжелые молотки могут увеличивать силу удара, что приводит к повышенному износу, в то время как более легкие молотки могут быть неэффективны при разрушении прочных материалов. Оптимизация веса молотка для обрабатываемого материала может продлить срок его службы.
- Форма молотка: Форма головки молотка также может влиять на скорость его износа. Например, определенные формы могут приводить к более равномерному износу или лучше подходить для определенных материалов, уменьшая чрезмерный износ.
5. Использование износостойких покрытий
Нанесение износостойких покрытий на молотки дробилок - проверенный способ продлить их срок службы. Эти покрытия обеспечивают дополнительный слой защиты от истирания, коррозии и высоких температур. Некоторые широко используемые покрытия включают:
- Покрытия из карбида хрома: Эти покрытия известны своей чрезвычайной твердостью и износостойкостью, особенно в условиях сильного абразивного износа.
- Керамические покрытия: Керамические покрытия часто используются благодаря своей способности противостоять износу и коррозии, обеспечивая долговременную защиту в сложных условиях.
- Полимерные покрытия: В некоторых случаях полимерные покрытия могут использоваться для защиты от коррозии и абразивного износа.
Нанесение износостойкого покрытия позволяет лучше защитить поверхность молота, что снижает скорость износа и продлевает срок его эксплуатации.
6. Правильная подача материала
Способ подачи материала в дробилку может повлиять на износ молотков. Чтобы уменьшить износ, важно подавать материал равномерно и с контролируемой скоростью. Слишком быстрая подача материала может вызвать излишнюю нагрузку на молотки, что приведет к их быстрому износу. Кроме того, в подаваемом материале не должно быть крупных и твердых предметов, таких как камни или металл, поскольку они могут повредить молотки и сократить их срок службы.
7. Техника дробления
Правильно выбранная технология дробления поможет повысить эффективность процесса и уменьшить износ молотков. Например:
- Постепенное дробление: Вместо того чтобы прогонять через дробилку сразу большое количество материала, используйте постепенный и контролируемый процесс дробления. Это снижает воздействие на молотки и минимизирует их износ.
- Предварительное дробление: Если материал слишком крупный или жесткий, рассмотрите возможность использования предварительной дробилки или других средств для его измельчения до приемлемого размера перед тем, как он попадет в молотковую дробилку.
8. Управление температурой
Высокие температуры могут ускорить износ молотков дробилок, особенно при работе с абразивными или липкими материалами. В некоторых случаях под воздействием высоких температур свойства материала молотка могут ухудшиться, что приведет к снижению производительности и сокращению срока службы. Механизмы охлаждения, такие как вентиляторы или системы охлаждения, помогают регулировать температуру и предотвращают перегрев, обеспечивая более долгий срок службы молотков.
9. Замена и ротация
Со временем, даже при надлежащем уходе, молотки придется заменить. Однако, регулярно поворачивая молотки и заменяя их до чрезмерного износа, вы можете предотвратить ненужные повреждения других частей дробилки. Многие дробилки имеют реверсивные молотки, которые можно вращать, чтобы продлить срок их службы.
Заключение
Увеличение срока службы молотков дробилок требует сочетания правильного выбора материала, регулярного технического обслуживания, оптимизированных методов работы и защитных покрытий. Тщательно продумав эти факторы и внедрив их в свою дробильную деятельность, вы сможете значительно снизить скорость износа молотков и повысить общую эффективность работы ваших дробилок. Это приведет к снижению эксплуатационных расходов, сокращению времени простоя и повышению производительности в долгосрочной перспективе.
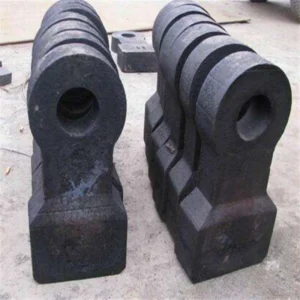
Почему стоит выбрать молотки для дробилок из легированной стали для обеспечения долговечности?
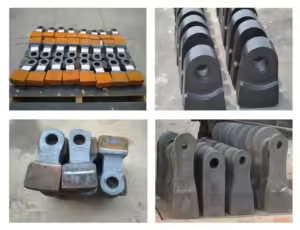
Как выбрать поставщика запчастей для молотковой дробилки
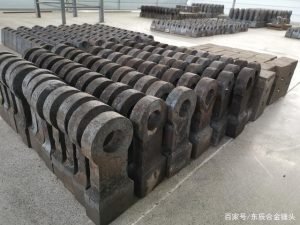
Типы молотков для дробилок: Что лучше для вашей машины?
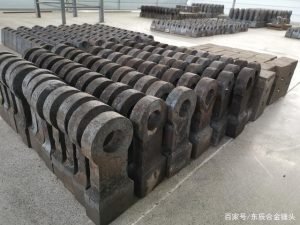
Что такое молотки-дробилки? Полное руководство для покупателей
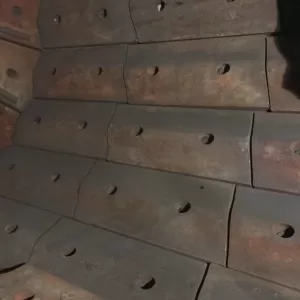
Как продлить срок службы футеровки шаровой мельницы
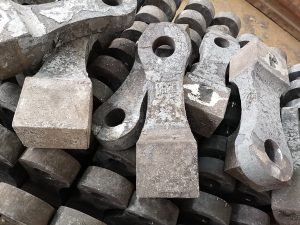